CONTENTS:
- Types of Motor Encoders by Their Construction
- What Should Be Considered When Choosing an Encoder for Your Motor System
- Types of Encoder's Mounting
In the era of industrial automation, lots of equipment was invented for fast and accurate measurements. Among various sensors, some encoders are designed for linear or angular movements. Their working process consists of fixing every movement or rotation and transmitting the actual position in real-time via digital or analog signals. 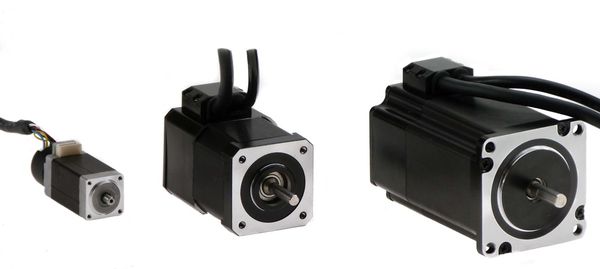
As electric motors are among the rotary types of equipment, it is a motor encoder that is needed for their positioning. It converts the angle of rotation of an object that is rotating (shaft) into electrical signals that allow you to determine the same angle of rotation (shaft), the direction of rotation and position relative to the axis. The need for this sensor arose in the search for new, more advanced methods of creating and operating well-known servo motors. The first was a pulsed magnetic servo motor encoder that determined the position of the rotor in a brushless DC motor (electronically commutated motor) system. The encoder, during rotation, produced pulses according to the number of poles of the magnet.
At the moment, by the type of action, we have at least three types of encoders:
- Magnetic;
- Magnetoresistor;
- Optical.
Along with encoders, temperature sensors are often used, since where it is mechanical or any other movement, friction and temperature rise occur, the values of which should not exceed permissible standards.
Types of Motor Encoders by Their Construction
By their construction, all encoders for motors could be divided into 2 big categoria: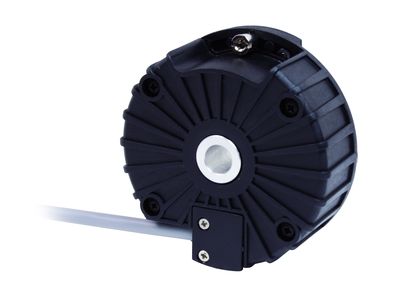
- Incremental encoders are simpler by their construction. An incremental encoder (aka a step encoder) consists of the following components: a light source, a disc with labels, a phototransistor assembly, and a signal processing circuit. The step encoder disc is subdivided into precisely positioned marks. The number of marks determines the number of pulses per revolution.
- Absolute encoders have more complex construction. In it, the infrared rays of the LED shine through the code disc and hit the phototransistor readout matrix located on the back of the code disc. At each step of the angular position of the code disk, its dark sections prevent light from entering certain phototransistors of the reading matrix that converts light signals into electrical ones. The electrical signals, in turn, are converted by the encoder electronics into binary code.
The first and the most important step in motor encoder's typology is the type of the motor itself.
It could be an AC motor, servo motor, DC motor or stepper motor.
- For AC motors, which are alternating current electric motors, in which the electric current in the rotor required to generate torque is obtained by electromagnetic induction from a magnetic field from the stator winding, as usual, incremental encoders are used. They help to stop the motor in a required position, changing the angle and position of equipment driven by a motor.
- DC motors produce magnetic field by their stator. For them, encoders are mostly used for speed control providing precise data about the motor's speed to the drive.
- A servo motor is a device based on an electric motor with negative feedback control. The use of servo drives allows achieving high levels of accuracy and repeatability of the processes for which they are responsible. Thanks to these features, servo drives are widely used in solving various industrial problems, in mechanical engineering and other industries. Due to their construction, for servo motors encoders, all types can be used including modular encoders, absolute and incremental ones. The choice basically depends on the accuracy of the signal required.
- Stepper motors are the most precise and cost-efficient. For their control, incremental encoders are used. They provide you with precise data in open-loop systems. Besides, encoders can provide you with information about the positioning of the motor's shaft in accordance with the step angle
What Should Be Considered When Choosing an Encoder for Your Motor System
When it comes to choosing encoders for a particular type of motor, there are a number of characteristics to consider. This applies primarily to the type of motor to be measured with the encoder.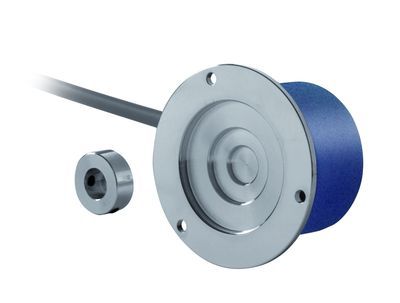
Also, an important feature is a way the encoder is mounted, since each individual model from manufacturers has its own characteristics for one or another type of installation. We will analyze it in more detail later.
What else should be considered when choosing encoders? Here is an approximate list of qualities that play a role in the selection of such industrial equipment.
- Signal type. Encoders provide information about the positioning of an object in the form of signals transmitted to the device. Older, albeit reliable, analog encoders use an analog signal for this. Analog encoders are popular due to their compatibility with many industrial controllers. The most common signals are 0-10 V and 4-20 mA. In this case, the voltage output is more susceptible to interference, wiring resistance. The current output is more resistant to electrical noise and has low signal loss when transmitting data over long cable runs. At the same time, they are being successfully replaced by industrial encoders with a digital signal. In addition to the accuracy of transmission, they are also compatible with modern industrial interfaces.
- Compatibility with industrial automation interfaces. While industrial systems are moving to full automation, it is important to select encoders that are suitable for interaction with the selected interface, for example, ProfiNet or ProfiBus compatible.
- The degree of protection is an equally important parameter. Especially if you are using the encoder under difficult operating conditions, such as elevated temperatures due to motor heating.
- Manufacturer. Despite the fact that such equipment is now offered by many manufacturers, quality and reliability are parameters that are not observed by all. If you want to get equipment that will work flawlessly, provide data with maximum accuracy and speed, it is better to give preference to proven brands presented in the Eltra catalog.
Types of Encoder's Mounting
In its simplest form, the encoder is connected to a counter programmed to measure the speed.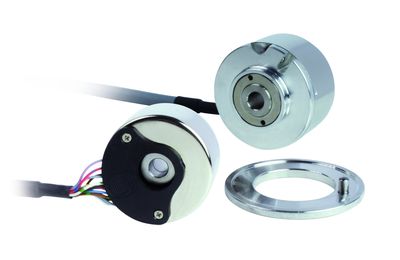
However, more often the work of the encoder is carried out together with the controller. An example is the rotation sensors on the shafts of motors that combine any parts with each other. Using calculations based on incoming data, the system monitors the gap between the parts. When a certain minimum value is reached, the registration of parts stops so as not to damage them.
Another case is the connection of encoders on motors with frequency converters, where they serve as feedback elements. Here the principle of how to connect a device is even simpler. The rotation angle sensor is connected to them using an interface board. This allows the motor speed and torque to be precisely maintained.
Summaries
Encoders are quite diverse devices in their construction, working principle and accuracy. To choose an appropriate model of the encoder for a motor drive, several features should be considered. These are the type of the motor, the type of the encoder itself, the type of mounting and even the protection level of the encoder. In Eltra, you are welcome to get a reliable and precise measurement tool for your industrial automation system, according to all these parameters.